Process of establishing a new partnership
Advantages of PVD
Vacuum coating technology has many advantages and, due to its development, is often the first choice over electroplating or powder coating. It is the first and only valid choice for many of applications due to the aesthetic effects and mechanical properties of PVD coatings, at a level unattainable by other methods
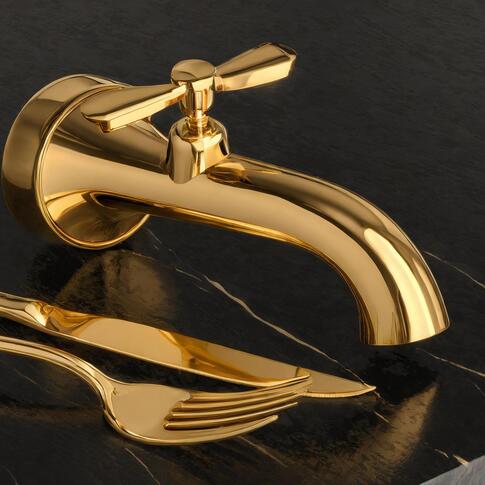
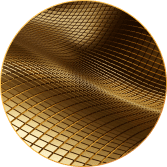
-
Higher mechanical resistance than other coatings
-
Higher corrosion resistance than other coatings
-
Higher scratch resistance than other coatings
-
Almost completely UV-resistant
-
Higher resistance to chemicals than other coatings
-
Very large variety of PVD coating colours
-
Perfect surface reproduction (matt, polish, brush)
-
Coatable on a wide range of materials
-
Coating of complex shapes possible
-
Coatings meet the special requirements of the food industry
-
Coatings meet the special requirements of the clinical industry
-
PVD coatings are a very environmentally friendly solution
Why it is worth to work with us
Market or tailor-made colours, even deep black
Our technologies enable the production of individual shades according to customer requirements or adaptation to colours available on the market today. Even deep black is also possible
Location in the centre of Poland (CEE region)
Our production centre is located in central Poland, right off the motorway. This makes production logistics with us a matter and cheap.
Preparation of pre-production samples
Before production, we prepare samples on the customer's components, so that when contracting further projects, the customer is certain of the result.
Short lead times - let's grow together
Short lead times mean lower storage costs and greater production flexibility. If order volumes increase, we will invest in new machinery, ensuring short lead times.
Colour stability throughout the piece
We ensure the greatest possible colour uniformity throughout the component. This is achieved by controlling virtually every process parameter, with the help of sophisticated electronics.
Special washing line
Thanks to our dedicated vacuum washing line, we reduce the amount of waste and defects on the surface. This translates into part quality and reduces customer costs.
Surface activation
In our process, we use surface activation, increasing the adhesion of the coating to the substrate, improving the properties of the resulting coating and greater homogeneity.
State-of-the-art R&D laboratory
Thanks to our laboratory, we have the opportunity to collaborate on the customer's product development by developing the required colour and coating properties.
FAQ
Below are the answers to the questions most frequently asked of our specialists.
PVD coatings generally have a higher mechanical resistance than other coatings. The hardness of PVD coatings, depending on the type, is in the range of 1500-2500HV.
PVD coatings, have very good corrosion resistance and are therefore very good for applications in aggressive environmental conditions (e.g. bathroom products). Depending on the quality of the coating, it also provides partial protection of the substrate against corrosion.
PVD coatings are characterised by their high resistance to UV radiation, and are therefore suitable for parts exposed to UV radiation, both for indoor and outdoor use. Their colour and properties remain practically unchanged over time.
Good-quality PVD coatings, thanks to their high adhesion and surface uniformity, are hardly reactive, making them highly resistant to the effects of various common cleaning detergents. One might be tempted to say that some PVD and PECVD coatings are practically completely unreactive.
reactive.
Depending on the targets and gases used, as well as the process parameters, a great variety of colours can be produced, e.g. gold, chrome, copper, bronze, deep black, gunmetal, mix colours (rainbow effect). These colours can be seen in our PVD coating applications section.
The visual effect (matt/polish/brush) depends on prior surface preparation. The PVD coating reflects the structure of the substrate due to its thickness (0.08um-4um). For examples of different surface finishes, see PVD coating applications.
The PVD coating process is usually the final surface treatment of the component. Due to the thinness of the coating (0.08um-4um), it perfectly replicates the previously prepared surface. However, in the case of coating plastic components, it is sometimes possible to additionally coat the component with a clear lacquer for additional protection.
In general, this depends on the volume of active plasma in the reaction chamber. The size of these chambers and the range of plasma action in decorative applications are larger than in technical applications, making it possible to coat even large parts. At Coating Factory we have 1000x1200mm equipment with a plasma operating range of 1200x1000mm (Height x Diameter).
Depending on the vacuum coating technology used, different types of material can be coated. Assuming the availability of the three technologies PVD (CAE), PVD (MS) and PECVD, it is possible to coat metals, plastics and ceramics (including glass). However, it should be noted that, depending on the type of substrate, coatings will have different mechanical properties (due to adhesion and process). Sometimes, for more demanding components, it may be necessary to lay down a galvanic interlayer before the surface is finished with a PVD coating
It is not possible to clearly define this. In the case of decorative solutions, however, the costs are so low that PVD coatings are finding their way into everyday items and the technology itself is being used more and more, also from an economic point of view.
The cost depends on a number of factors, these are:
- the size of the elements to be PVD-coated (this determines how many will fit into the process)
- the base material of the PVD coating component
- the expected mechanical properties of the PVD coating
- the expected colour of the PVD coating
At first glance, the processes appear similar, but PVD hard coatings have far superior mechanical and resistance properties. With hard PVD coatings, it is also possible to achieve a wider range of colours. The PVD hard coating process is usually a reactive process, involving the deposition of a special ceramic layer (e.g. TiN). In the case of metallization, it is usually the evaporation of the metal and its deposition on the coated component. In general, the main differences between these technologies are the process time, the type of source being vapourised and the fact that metallization
There is no single answer to this question, it all depends on the application of the coated component. However, due to the special properties of the hard coatings
PVD as well as the purity and eco-friendliness of the process, it is increasingly the technology of choice and in some areas already accounts for the vast majority of applications. The much greater colour possibilities of PVD and PECVD coatings compared to electroplating are also a major advantage. Due to the increasing environmental requirements of electroplated coatings, the PVD process is often the cheaper solution. The biological versatility of PVD and PECVD coatings also allows their widespread use in the food and clinical industries.
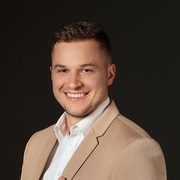
Waldemar Furman
PVD specialist
Talk with us about
Your application
Sochaczewska 46/50
99-400 Łowicz, Poland
Test our coatings
on your components!
Send us samples and we will coat them.