Applications of PVD and PECVD coatings
Due to the exceptional aesthetic and mechanical properties of PVD and PECVD hard coatings, they have a wide range of applications. As these technologies continue to develop and improve, their use is becoming more widespread. The durability, aesthetics and environmental friendliness of coatings obtained by high-vacuum methods mean that PVD and PECVD coating services have permanently replaced powder coating and electroplating in many industrial sectors.
PVD and PECVD coatings
for the bathroom industry
Main technologies: PVD (CAE), PVD (MS),
Ceramic fittings are a very large sector which, due to the high resistance and aesthetic properties of PVD coatings, has chosen this method of coating as its primary surface finish.
The wide colour range and texture mapping by PVD (CAE) coating make it possible to achieve the effects expected by the consumer market. In addition, PVD (MS) or PECVD methods make it possible to coat plastic parts (ABS) in the same shade as metal fittings.
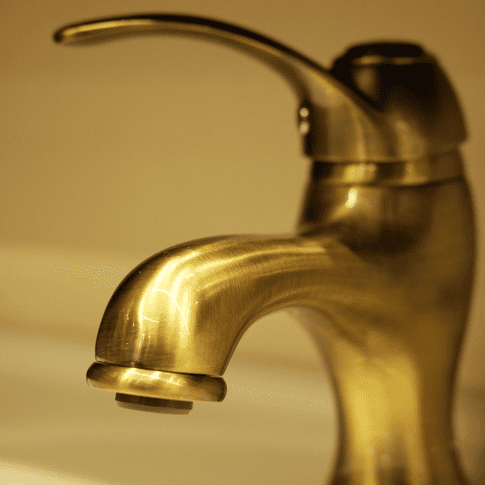
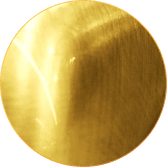
PVD and PECVD coatings for
door and window elements
Main technologies: PVD (CAE), PVD (MS)
In the industrial sector of doors, windows and hinges, PVD coatings are also finding increasing use. Today, door fittings are able to make a significant contribution to interior design.
Deep black, gold or copper colours are ideal for application to door hardware. The PVD coating applied to handles is not only highly durable, but also allows different surface finishes to be achieved. Different colours in matt, polished or brushed are therefore possible.
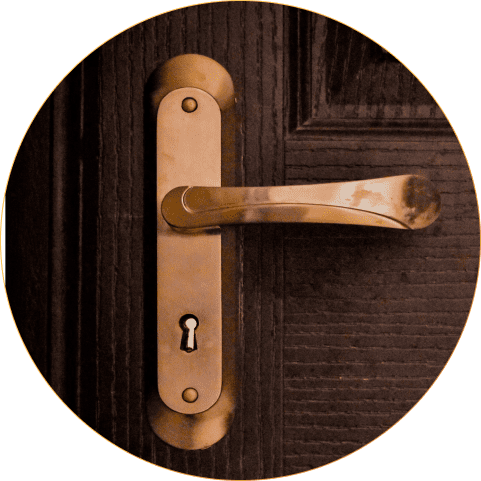
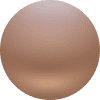
PVD and PECVD coatings for
for the food industry
Main technologies: PVD (CAE)
The food industry has high requirements for the surface finish of components for two reasons. Aesthetic, and compliance with food contact approval.
As PVD coatings are coatings of very high purity and homogeneity, there is virtually zero chance of contamination. In addition, they are neutral compounds (usually ceramic coatings). Combined with the decorative aspect of the PVD finish, it is the ideal treatment for the food industry.
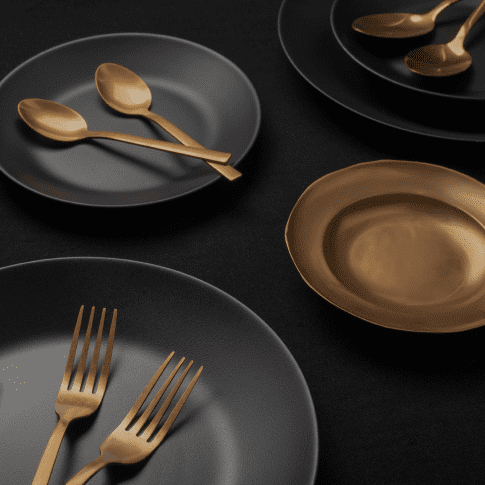
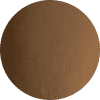
PVD and PECVD coatings for
components of the furniture industry
Main technologies: PVD (CAE), PVD (MS)
The furniture industry is another sector that is a significant beneficiary of the development of vacuum technology. Thanks to the advantages of PVD coatings, it is possible to finish the surface of furniture components with previously unavailable surface smoothness and durability.
Due to their UV and corrosion resistance, PVD coatings are very suitable for outdoor furniture. The high mechanical strength, on the other hand, means that furniture handles do not wear out quickly during use.
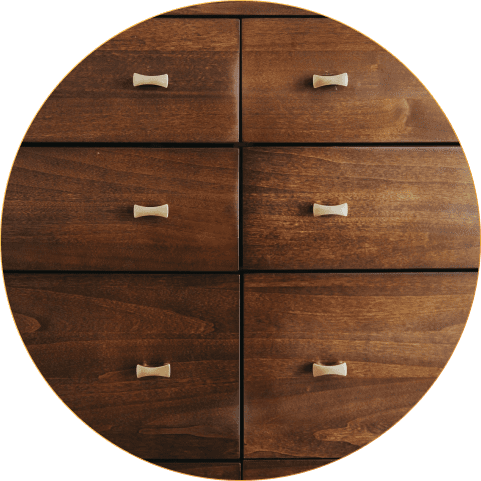
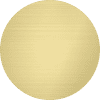
PVD and PECVD coatings for
elements of the funeral industry
Main technologies: PVD (CAE)
The funeral industry rarely comes to mind as the first thought when it comes to decorative applications, but in practice this is not the case. Many of the elements used in tombstone decoration require a durable and elegant finish.
PVD coatings are the ideal coating for gravestone elements due to their high weather resistance. They are UV-resistant, non-corrosive and have a wide colour spectrum. It is therefore possible to create inscriptions or crosses in the entire palette possible with PVD technologies.
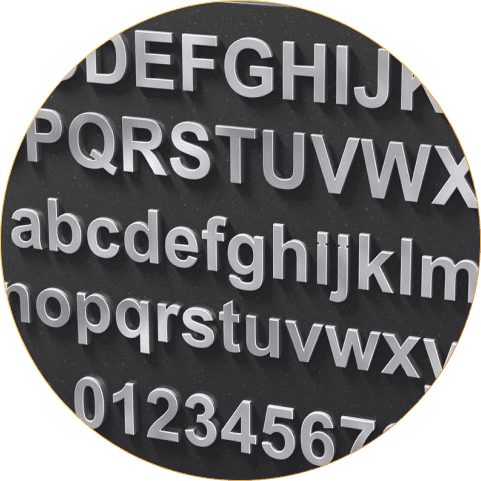
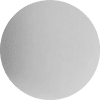
PVD and PECVD coatings for
for the lighting industry
Main technologies: PVD (CAE), PVD (MS)
The lighting industry is also benefiting from the development of vacuum technology. PVD coatings not only provide an excellent surface finish for lighting components, but also offer durability and resistance to a range of external factors.
Thanks to the use of PVD coatings, lamps and peripheral accessories can be finished with a surface of unprecedented smoothness, which contributes to aesthetics and ease of maintenance. In addition, UV resistance means that PVD-coated components can be used both indoors and outdoors, retaining their original appearance for a long time.
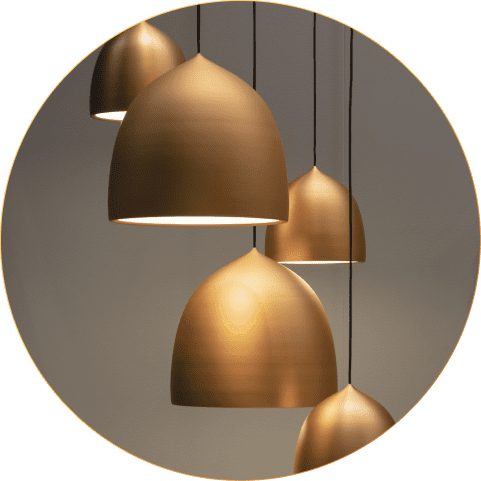
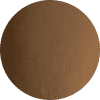
PVD and PECVD coatings for
bicycle, motorbike and automobile components
Main technologies: PVD (CAE), PECVD
The bicycle, motorbike and automotive industries are broad sectors that use PVD and PECVD coatings both decoratively and technically. Thus, it is possible to achieve exceptional visual effects as well as durable functional solutions.
DLC coatings are ideal for components such as shock absorber lags, giving them a nice aesthetic effect as well as excellent tribological properties. The high mechanical resistance of PVD and PECVD coatings also makes it possible to use them on bicycle pedals or brake levers, ensuring an original appearance and abrasion resistance.
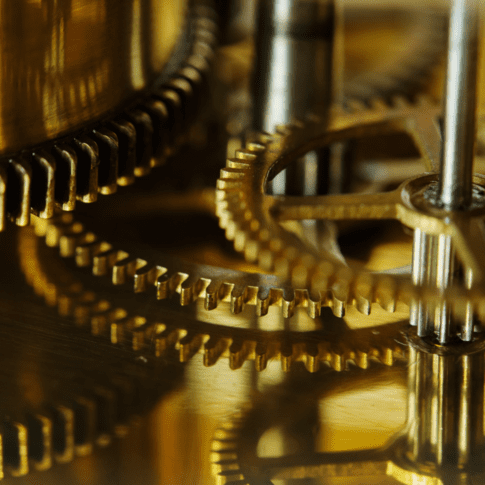
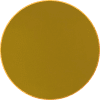