High-vacuum
coating technologies
High vacuum coating is a technology that applies thin coatings to the surface of an object under high vacuum (10^-5) conditions. Often abbreviated as PVD or PECVD technology.
The component to be coated is placed in a heated chamber in which pressure is reduced during the process and the required temperature is maintained. Once the required vacuum and temperature levels are reached, the coating deposition process begins, the details each process depend on the technology chosen
PVD – Physical Vapor Deposition
PVD – Physical Vapor Deposition, is one of the methods of high vacuum deposition of coatings. We can divide it into two types depending on how the source material is excited PVD (CAE) and PVD (MS). Depending on your expectations of the properties and colour of the coating, a specific vacuum deposition method will be more or less suitable. At Coating Factory, we are the only one in the local market to have both of these technologies (as well as PECVD described below).
PVD (CAE): Cathodic Arc Evaporation Process
The PVD (CAE) process is based on the evaporation of a source by an electric arc. It is the most widely used process in decorative PVD coating. In this process, an electric arc travels across the surface of a metal target (source) causing it to vaporise.
The PVD (CAE) process is carried out at relatively high temperatures (in the range of 150-300°C) and is the fastest of the three processes described, which is a major advantage leading to its widespread use in the deposition of coatings on metal components, as the process is very effective qualitatively and economically. Due to the high process temperatures and evaporation characteristics of the source, the deposition of coatings by the PVD process (CAE) on plastics is severely limited, so that PVD (MS) and PECVD technologies are recommended for these materials.
This is a process that allows standard PVD coating colours such as gold, chrome, copper and their derivatives to be covered up to dark grey.
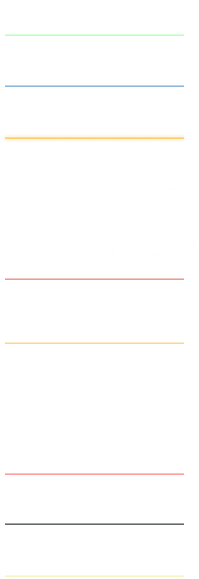
PVD (MS): Magnetron Sputtering process
The PVD (MS) process is based on the excitation of a target (source) by bombarding it with excited gas ions (usually argon).
The vapourisation of the material thus occurs by kinetic action between individual gas ions and metal atoms from the surface of the target.
Due to the milder excitation characteristics of the PVD (MS) process, the process can take place at a lower temperature (even room temperature) and the excited plasma is more homogeneous. This translates into the fact that PVD (MS) technology is better for applying coatings to plastics. For coatings obtained by PVD (MS), the coatings are smoother (have less roughness) relative to the CAE process. Operating at a lower temperature and more subtle excitation of the source, results in longer process times, making the CAE process cheaper relative to MS for standard applications and colours.
Advantages of PVD (MS) coatings include the more deep colours, lower roughness, “soft touch effect”, or simply the fact that they can be successfully applied to decorative-utility components made of plastic, ceramics and, of course, metal.
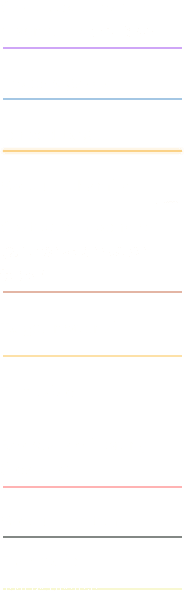
PECVD – Plasma Enhanced Chemical Vapour Deposition
PECVD – Plasma Enhanced Chemical Vapour Deposition, is another of the high vacuum deposition methods for coatings. Thanks to a completely different way of delivering the reactants into the chamber, this technology allows more stoichiometrically complex coatings to be produced, including in particular DLC (Diamond Like Carbon) coatings. Again, as Coating Factory, we are the only one in the local market with PECVD technology for large-scale decorative applications.
PECVD: Plasma Enhanced Chemical Vapour Deposition
In the PECVD process, the source of material for the coating to be deposited is, gas entering the chamber. This gas is decomposed by supplying a large amount of energy by passing it through a plasma.The precursors supplying the elements needed to form the expected coating are therefore various gases.
A definite advantage of this technology is the possibility to produce coatings containing carbon, otherwise known as DLC coatings, which, as in the case of black coatings produced using the PVD (MS) method, can have a very deep black colour, low roughness or a “soft touch” effect. However, a particular difference is the durability of DLC coatings; their high strength and low coefficient of friction means that they are not only used in decorative applications, but also in functional applications where good tribological properties are required.
The reactants from the introduced gas (precursor) are very uniformly distributed in the chamber, so that very geometrically complex shapes can be coated in the PECVD process, with high surface uniformity and strength.
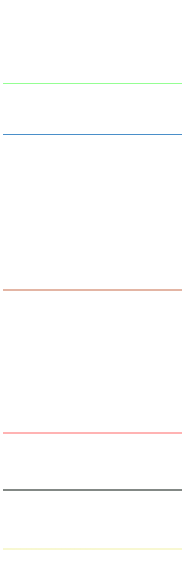
Quality control and internal R&D
Quality control and laboratory testing at Coating Factory are carried out in several stages. The analysis of each coated component is carried out during the various stages of production, starting from the inspection at the entrance to the inspection at the packaging of the components for dispatch.
In order to maintain production stability, we also carry out colour checks on production batches. We also systematically carry out a thorough analysis of the mechanical properties of the colour of manufactured coatings using reference samples coated in the same production process.
Highlights of the solutions used at CoatingFactory
Market or tailor-made colours, even deep black
Our technologies enable the production of individual shades according to customer requirements or adaptation to colours available on the market today. Even deep black is also possible
Touch-free cleaning and surface activation
Thanks to our dedicated washing line, each component is cleaned before coating, thus reducing the amount of waste and defects on the surface.
Precise process control
Precise process control enables high production repeatability, the production of unique coating colours and the coating of different types of materials. It also enables high colour uniformity.
DLC coatings
PECVD technology allows us to produce special coatings, of the DLC type. These are 'diamond like carbon' coatings with particularly high strength and visual properties.
Soft touch effect
It is possible to create a "soft touch" effect - this makes the black PVD coating look and feel softer to the touch than the painted coating
Large rectangular targets
The solution used makes it possible to achieve a more homogeneous plasma throughout the chamber, allowing a more uniform colour coating.
Multiple technologies in one company
Thanks to our range of technologies, we can create colours that are unique on the market, as well as coating more complex components.
Highly educated and specialised staff
Our equipment is operated and serviced by highly educated staff. This ensures a consistent level of quality and clear, direct cooperation.
FAQ
services. Below are the answers to the questions most frequently asked
of our specialists.
PVD (CAE), PVD (MS) and PECVD are non-competing technologies. None of them is clearly best for everything. Choosing the right technique depends on the final application of the coated product. For example, PVD (CAE) has definite advantages for the serial production of gold decorative coatings, while for deep black, PVD (MS) or PECVD methods are better options.
Yes – due to the thinness of PVD coatings and the nature of their application, any contamination of the component prior to coating will result in a defect. These can be visual defects, or more difficult to detect mechanical defects. In the case of visual defects, it is better because they can be seen quickly. Mechanical defects, on the other hand, can cause the parts to lose their original appearance over a short period of time, which may leave the consumer dissatisfied – which is why it is so important that PVD coatings have the right level of quality.
In order to ensure a good cooperation, it is best that the parts transferred to us are packed in standard containers. Different items should not be mixed in one package (e.g. two different batteries in one box) to avoid logistical problems. No safety stickers should be affixed. It is also important that the parts are cleaned of oil and are not dusty.
All of the above can make the standard process more difficult and costly. However, everything is a question of the capabilities of each party and individual arrangements can be made if necessary.
For decorative coatings, standard cycles are in the range of 1-2h. This depends on the colour, the expected quality of the coating and the geometry of the parts to be coated. Sometimes certain companies practice shorter cycles in order to generate savings, because in some cases it is difficult to verify at first glance, thus passing visual quality control. However, the problems come out over time, because a coating produced with too short a cycle (bypassing important process steps), will last much less. Often with short cycles there is a problem with colour uniformity and shade.
Depending on the sources and gases used, as well as the process parameters, very different colours can be produced, e.g. gold, chrome, copper, bronze, deep black, gunmetal, colour mix (rainbow effect). More You can see in our applications site.
The first difference is that DLC (Diamond-like carbon) coatings are obtained using the PECVD process, which differs from the PVD process. This is described in detail under PVD technologies. DLC coatings contain carbon in their composition, enabling the formation of SP2 and SP3 bonds – depending on their proportion, they have different properties. The special features of DLC coatings are:
- extremely high hardness (up to 3000 HV)
- reduced adhesive wear
- Low coefficient of friction
- very deep black colour can be achieved (coefficient l=28, CIElab)
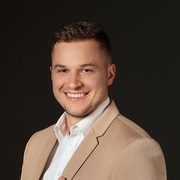
Waldemar Furman
PVD specialist
Talk with us
about your products
Sochaczewska 46/50
99-400 Łowicz, Polska
Do You want to know
more about tecnology?
We will be happy to answer any questions