Technologia PVD i PECVD
Nanoszenie twardych powłok PVD i PECVD to technologie polegające na nakładaniu cienkich powłok na powierzchnię przedmiotu w warunkach wysokiej próżni (10^-5). Często skrótowo po prostu nazywane „PVD”, co jest dużym skrótem myślowym – bo technologia ta ma wiele odmian.
Generalnie powlekany przedmiot umieszczany jest w ogrzewanej komorze, gdzie w trakcie procesu redukuje się ciśnienie i utrzymuje wymaganą temperaturę. Po osiągnięciu wymaganego poziomu próżni i temperatury, rozpoczyna się proces osadzania powłok, którego szczegóły zależą od wybranej techniki PVD.
Rodzaje PVD – o metodach nanoszenia powłok PVD
PVD – skrót od Physical Vapor Deposition, to jedna z technik wysokopróżniowego osadzania powłok z fazy gazowej. Rodzaje powłok PVD można rozdzielić w zależności od sposobu wzbudzenia materiału źródłowego i reaktywności procesu. Metody powlekania twardymi powłokami PVD to procesy reaktywne czyli PVD (CAE) i PVD (MS). Powłoki otrzymane procesami reaktywnymi mają większą trwałość względem niereaktywnej metalizacji próżniowej. Tak więc w zależności od oczekiwań co do właściwości i barwy, konkretne rodzaje nanoszenia powłok będą mniej lub bardziej odpowiednie.
W Coating Factory jako jedyni na rynku lokalnym posiadamy oba rodzaje nanoszenia twardych powłok PVD (a także PECVD opisane poniżej).
PVD (CAE): Cathodic Arc Evaporation Process
Proces PVD (CAE) oparty jest na odparowywaniu źródła łukiem elektrycznym. Jest to najczęściej stosowany proces w dekoracyjnym powlekaniu PVD. W tym procesie łuk elektryczny porusza się po powierzchni metalowego targetu (źródła) powodując jego odparowanie.
Proces PVD (CAE) przebiega we względnie wysokiej temperaturze (w zakresie 150-300°C) i jest to najszybszy z trzech opisywanych procesów, co stanowi jego dużą zaletę powodującą powszechne zastosowanie w osadzania powłok na elementach z metalu, ponieważ proces jest bardzo efektywny jakościowo i ekonomicznie. Ze względu na wysokie temperatury procesu i charakterystykę odparowania źródła osadzanie powłok procesem PVD (CAE) na tworzywach sztucznych, jest mocno ograniczone, przez co do tych materiałów zalecane są technologie PVD (MS) i PECVD.
Jest to proces pozwalający na pokrycie standardowymi kolorami pokryć PVD, takimi jak złoty, chrom, miedziany i ich pochodne, aż do ciemnej szarości.
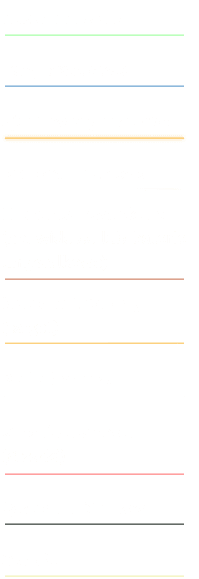
PVD (MS): Magnetron Sputtering process
Proces PVD (MS) polega na rozpylaniu targetu (źródła) poprzez bombardowanie go wzbudzonymi jonami gazu (najczęściej argonu). Odparowanie materiału następuje więc w wyniku działania kinetycznego pomiędzy pojedynczymi jonami gazu a atomami metalu z powierzchni targetu.
Dzięki łagodniejszej charakterystyce wzbudzenia w procesie PVD (MS), proces może zachodzić w niższej temperaturze (nawet pokojowej), a wzbudzona plazma jest bardziej jednorodna. Przekłada się to na fakt że technologia PVD (MS) jest lepsza do nakładania powłok na tworzywa sztuczne. W przypadku powłok otrzymanych metodą PVD (MS), powłoki te są gładsze (mają mniejszą chropowatość) względem procesu CAE. Działanie w niższej temperaturze i bardziej subtelne wzbudzenie źródła, powoduje wydłużenie czasu procesu, przez co w przypadku standardowych aplikacji i kolorów proces CAE jest tańszy względem MS.
Zalety powłok otrzymanych procesem PVD (MS) to m.in. efekt większej głębi koloru, niższa chropowatości, efekt “soft touch”, czy po prostu fakt, że z powodzeniem można je nakładać z na elementy dekoracyjno-użytkowe zrobione z plastiku, ceramiki i oczywiście metalu.
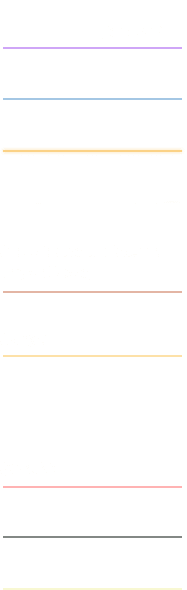
PECVD – chemiczne osadzanie z fazy gazowej ze wspomaganiem plazmowym
PECVD – skrót od Plasma Enhanced Chemical Vapour Deposition, to kolejna z metod wysokopróżniowego osadzania powłok. Jest to chemiczne osadzanie z fazy gazowej ze wspomaganiem plazmowym. Powszechnie powłoki otrzymane tą metodą także nazywane są powłokami PVD co jednak z punktu widzenia technicznego jest błędem. Dzięki całkiem innemu sposobowi dostarczania reagentów do komory, technologia ta pozwala na wytworzenie bardziej skomplikowanych stechiometrycznie powłok, w tym w szczególności powłok DLC (Diamond Like Carbon). Także w tym przypadku jako Coating Factory jako jedyni na rynku lokalnym posiadamy technologie PECVD zastosowań dekoracyjnych w dużej skali.
PECVD: Plasma Enhanced Chemical Vapour Deposition
W procesie PECVD źródłem materiału dla osadzanej powłoki jest, gaz wpuszczany do komory. Gaz ten jest rozkładany w wyniku dostarczenia dużej ilości energii poprzez przepuszczenie go przez plazmę. Prekursorem dostarczającym pierwiastki potrzebne do wytworzenia oczekiwanej powłoki są więc różnego rodzaju gazy.
Zdecydowaną zaletą tej technologii jest możliwość wytwarzania powłok zawierających węgiel, inaczej zwanych powłokami DLC, które podobnie jak w przypadku czarnych powłok wytwarzanych metodą PVD (MS), mogą posiadać kolor bardzo głębokiej czerni, niską chropowatość czy efekt “soft touch. Jednak szczególną różnicą są właściwości wytrzymałościowe powłok DLC, ich wysoka wytrzymałość i niski współczynnik tarcia powoduje że nie tylko znajdują swoje miejsce w aplikacjach dekoracyjnych, ale także funkcjonalnych gdzie wymagane są dobre właściwości tribologiczne.
Reagenty pochodzące z wprowadzonego gazu (prekursora) są bardzo równomiernie rozprowadzone w komorze, dzięki czemu w procesie PECVD możliwe jest pokrywanie bardzo skomplikowanych geometrycznie kształtów, z zachowaniem dużej jednorodności i wytrzymałości powierzchni.
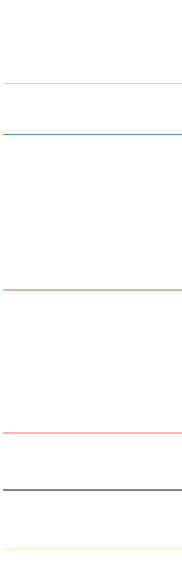
Kontrola jakości i wewnętrzne B+R
Kontrola jakości i badania laboratoryjne w Coating Factory wykonywane przez nas usługi kontrolujemy wieloetapowo. Analiza każdego pokrywanego elementu dokonywana jest w trakcie poszczególnych etapów produkcji zaczynając od inspekcji na wejściu, aż po kontrolę przy pakowaniu elementów do wysyłki.
W celu utrzymanie stabilności produkcji prowadzimy tez kontrole barwy serii produkcyjnych. Systematycznie przeprowadzamy też dokładną analizę właściwości mechanicznych barwę produkowanych powłok wykorzystując w tym celu próbki referencyjne powlekane w tym samym procesie produkcji.
Co wyróżnia rozwiązania stosowane w CoatingFactory
Kolory indywidualne, obecne na rynku , a nawet głęboka czerń
Pposiadana technologia umożliwia produkcję indywidualnych odcieni zgodnie z oczekiwaniami klienta lub dostosowanie się do kolorów z rynku. Możliwe jest także wykonanie koloru głębokiej czerni
Bezdotykowe mycie i aktywacja powierzchni
Dzięki posiadanej przez nas dedykowanej linii myjącej każdy element przed pokryciem jest czyszczony, dzięki czemu zmniejszamy ilość odpadu i defektów na powierzchni
Dokładne sterowanie procesem
Dokładne sterowanie procesem umożliwia dużą powtarzalność produkcji, produkcję unikatowych kolorów powłok i pokrywanie różnego rodzaju materiałów. Umożliwia też zachowanie wysokiej jednorodności barwy.
Powłoki DLC
Technologia PECVD pozwala nam na produkcję szczególnych powłok, typu DLC. Są to powłoki “diamond like carbon”, posiadające szczególnie wysokie właściwości wytrzymałościowe i wizualne.
Efekt soft touch
Mozliwe jest wytworzenie efektu “soft touch” - powoduje to, że czarna powłoka PVD wygląda i wydaje się być miększa w dotyku, niż malowana powłoka
Duże prostokątne targety
Stosowane rozwiązanie umożliwia osiągnięcie bardziej jednorodnej plazmy w całej komorze, co pozwala na bardziej jednorodne kolorystycznie powlekanie.
Wiele technologii w jednej firmie
Dzięki posiadanemu zakresowi technologii, możemy tworzyć wyjątkowe na rynku kolory, a także powlekać bardziej skomplikowane elementy.
Wysoce wyspecjalizowana kadra
Nasze urządzenia obsługiwane i serwisowane są przez wysoce wykształconą kadrę. Dzięki czemu zapewniamy stały poziom jakości i klarowna, bezpośrednią współpracę.
FAQ
Poniżej przedstawiamy odpowiedzi na pytania najczęściej zadawane naszym specjalistom.
Technologie PVD (CAE), PVD (MS) i PECVD to technologie niekonkurujące ze sobą. Żadna z nich nie jest jednoznacznie najlepsza do wszystkiego.Dobór odpowiedniej techniki zależy od finalnego zastosowania produktu powlekanego.
Dla przykładu PVD (CAE) posiada zdecydowane zalety w przypadku seryjnej produkcji złotych powłok dekoracyjnych, natomiast do głębokiej czerni lepszym rozwiazaniem są metody PVD (MS) lub PECVD.
Tak – ze względu na niewielką grubość powłok PVD i specyfikę ich nakładania, każde zanieczyszczenie elementu przed powleczeniem, będzie skutkować defektem. Mogą to być defekty wizualne, lub trudniejsze do wykrycia defekty mechaniczne.
W przypadku defektów wizualnych jest o tyle lepiej, że da się je szybko zauważyć. Defekty mechaniczne mogą natomiast spowodować że elementy straci swój pierwotny wygląd w niedługim okresie czasu przez co konsument może być niezadowolony – dlatego tak ważne jest aby powłoki PVD posiadały odpowiedni poziom jakości.
W celu zapewnienia dobrej współpracy, najlepiej aby przekazywane nam częsci były pakowane w standardowe pojemniki. Nie powinno się mieszać różnych elementów w jednej paczce (np. dwóch różnych baterii w jednym pudełku), aby uniknąć problemów logistycznych. Nie należy naklejać żadnych naklejek zabezpieczających. Ważne jest także, aby części były oczyszczone z oleju i nie były zapylone.
Wszystko powyższe może spowodować utrudnienia w standardowym procesie, a także zwiększać jego koszty. Wszystko jest natomiast kwestią możliwości każdej ze stron i w razie potrzeby istnieje możliwość ustaleń indywidualnych.
W przypadku powłok dekoracyjnych standardowe cykle trwają w zakresie 1-2h. Jest to zależne od koloru, oczekiwanej jakości powłoki i geometrii powlekanych elementów.
Zdarza się, że pewne firmy praktykują krótsze cykle aby wygenerować oszczędności, ponieważ w niektórych przypadkach jest to ciężkie do zweryfikowania na pierwsze rzut oka, tym samym przechodzi to wizualną kontrolę jakości. Problemy jednak wychodzą z czasem, ponieważ powłoka wytwarzana w zbyt krótkim cyklu (z pominięciem ważnych etapów procesu), będzie znacznie mniej trwała. Często przy krótkich cyklach jest problem z jednorodnością koloru i jego odcieniem.
W zależności od stosowanych źródeł i gazów, a także parametrów procesu możliwe jest wyprodukowanie bardzo zróżnicowanych kolorów, np. złoto, chrom, miedź, brąz, głęboka czerń, gunmetal, mix kolor (efekt tęczy). Wiecej kolorów można zobaczyć w zakładce z zastosowaniami powłok PVD i PECVD.
Pierwszą różnicą jest to, że powłoki DLC (Diamond-like carbon) otrzymywane są w procesie PECVD, który różni się względem procesu PVD. Dokładnie jest to opisane w zakładce Technologie PVD. Powłoki DLC w swoim składzie zawierają węgiel, umożliwiający tworzenie wiązań SP2 i SP3 – w zależności od ich proporcji posiadają one różne właściwości. Szczególne cechy powłok DLC to:
- ekstremalnie wysoka twardość (aż do 3000 HV)
- zmniejszone zużycie adhezyjne
- niski współczynnik tarcia
- możliwośc osiągnięcia koloru bardzo głębokiej czerni (współczynnik l=28, CIElab)
- proces wytwarzania powłok PECVD (w tym DLC) jest droższy niż standardowe osadzanie powłok PVD
Poniżej krótka odpowiedź, a pod linkiem bardziej szczegółowy artykuł: coatingfactory.pl/pvd-a-metalizacja-pvd
Na pierwszy rzut oka procesy te wydają się podobne ponieważ oba to według terminologii metody PVD – czyli fizyczne osadzanie z fazy gazowej.
Różnice są więc dalej. Proces nanoszenia twardych powłok PVD jest procesem reaktywnym, polegającym na osadzeniu specjalnej warstwy ceramicznej (np. TiN). W przypadku metalizacji próżniowej jest to odparowanie metalu i osadzenie go na elemencie powlekanym (czyli przeniesienie z punktu A do B, bez reakcji). Głównymi różnicami pomiędzy tymi technologiami jest czas procesu, rodzaj naparowywanego źródła i to czy zachodzi w komorze reakcja lub nie.
Nakładanie twardych powłoki PVD daje lepsze właściwości mechaniczne i odpornościowe otrzymanych warstw, kosztem czasu procesu. W przypadku twardych powłok PVD możliwe jest także osiągnięcie szerszej gamy kolorów.
Ze względu na czas trwania nakładania twardych powłok PVD, usługi te są droższe niż metalizacja PVD. Nie są to jednak metody bezpośrednio konkurencyjne ponieważ pokrycia zdecydowanie różnią się trwałością.
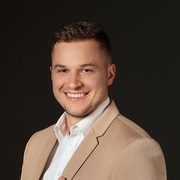
Waldemar Furman
Sprzedaż i Marketing
Porozmawiaj z nami
o swojej aplikacji
Sochaczewska 46/50
99-400 Łowicz, Polska
Interesują Cię szczegóły?
Chętnie odpowiemy na wszystkie pytania